Offshore 3D Laser Scanning
Versatility in many challenging applicatieons
Surveying is benefiting from continually evolving new technologies. One is 3D laser scanning, which is often used for measurements in complex industrial installations such as pipeline-rack crossings or entire petrochemical installations. Laser scanning is also increasingly being used in the field of prototyping and cultural heritage. In fact, it is safe to assume that this technology will be beneficial in any challenging environment, or for complex shapes.
Laser scanners emit a narrow laser beam and then receive and process the signal returned by reflection from the object. Depending on the model selected, laser scanners can measure between 100 and 500,000 points per second. The range varies between 20 and 100 metres, with an accuracy of between ± 1mm and 5cm. The devices generate a ‘point cloud’ of hundreds of thousands of surveyed points. These in turn can be used to create an exact but rudimentary 3D model of the object, which can be converted by software into a fully-fledged 3D model, recognisable by anyone. It is this processed 3D model that may ultimately be used for countless applications.
The Technology
The technique is ideally suited for rapid and detailed non-contact measurement and mapping; the 3D image obtained can then be analysed and edited off-site. The method is particularly suitable for modelling highly complex sites and objects made up of irregular shapes. Scanning results in an extremely accurate representation of the object, and offers the considerable advantage of enabling even objects that are difficult or impossible to access still to be modelled.
The laser-scanning technique consists of capturing data in the field, processing it and often creating 3D modelling for a CAD model, providing accurate and up-to-date spatial in- formation. To perform these steps various software packages are available. Today’s laser-scanning hardware and processing software are very good, but a challenge remains there for the software developers to improve the modelling software to come from the point-cloud to a finalized 3D CAD model. This is still a more or less labour-intensive process, depending on the accuracy and detail the client needs in the CAD model. Some software packages recognise some structures (piping, steel etc) so these can be designed semi-automatically. For more complex structures, additional drawing is needed.
In this article we will examine a specific case in which laser scanning is used in a project executed by Globe NV in Belgium. Globe has used this technology in the creation of 3D models not only for industrial plants in the chemical and energy industries but also for works of art, historic buildings and archaeological sites, ships under construction and many other structures. Recently the Globe team went offshore for the first time, to an innovative deep-water oilfield in the Gulf of Guinea, 150km off Angola in West Africa.
The Girassol Oilfield
The FPSO Girassol is the world’s largest ‘Floating Production, Storage and Offloading vessel’. With a hull 300m long, 60m wide and 30m deep, this ship-like vessel is permanently but flexibly moored to sixteen ‘suction anchors’ on the unstable seabed in 1,350 metres of water 210km north-north-west of Luanda, the capital of Angola. The vessel is connected to a large number of drilling platforms pumping oil from the gigantic Girassol reservoir, some 1,200 metres beneath the seabed. Together these wells currently supply some 200,000 to 250,000 barrels of crude oil daily, through pioneering ‘riser towers’ four times the height of the Eiffel Tower, also secured on the seabed by means of suction anchors. The FPSO has a storage capacity of 2 million barrels of crude, and a processing capacity of 200,000 barrels per day. The crude oil, after sufficient preliminary processing for shipment to its destination, is pumped into a tanker approximately once each week.
The operators of FPSO Girassol, Total Exploration Production Angola, now wish to exploit new oilfields in the vicinity, entailing a doubling of production and processing capacity onboard the existing vessel. This necessitates new plant and piping routes within an already crowded environment. Globe was commissioned to carry out laser-scanning in order to determine whether the proposed new modules will fit the available space, to plan new piping routes and to determine where new reinforcements for existing steel structures could be placed.
The task entailed checking whether the original Plant Design System (PDS) model of the FPSO matched the new (as-built) measurements, followed by adjusting the model to the as-built situation wherever discrepancies exceed 50mm. This was required both for the steelwork and for all piping of diameter 15mm and more and flanges of thickness 10mm and more. To plan this work in advance the team had to examine the existing model to identify critical areas, priorities and bottlenecks, and select appropriate scanner-station
positions. In order to control deformations and eliminate as far as possible the static and dynamic distortions of the ship, each scanning area was limited to a maximum range of 40 metres. Seven reference frames were established for seven different areas within the vessel and all were linked and oriented to the coordinate system for the FPSO as a whole.
Survey Team at Work
The survey team consisted of two surveyors from Globe NV, together with two local assistants, using reflectorless total station and Trimble S25 and GS100 laser scanners. The bulk of the scanning was carried out using the GS100 instrument, although the S25 was used for some 10% of the work. Available software included Trimble RealWorks Survey, Pointscape, 3Dipsos and MicroStation TriForma. During the seventeen days spent onboard, 101 flat adhesive targets were measured in ship coordinates using the total station so as to provide control for laser scanning from around seventy different scanner stations; a total of more than 100 million points were scanned. The resulting accuracy, after combining all the individual models in RealWorks Survey software, was of the order of ± 20mm.
This was the first time that Globe had used this technique on a ship at sea. Under normal circumstances both the laser scanner itself and the objects being scanned would be assumed completely immobilised during measurement: it is obvious that this was not the case here. Difficulties encountered included dramatic ‘static’ deformations caused by loading and unloading the vessel in the course of the job, as well as the expected dynamic deformations caused by waves and associated motion of the ship. In addition, continuous operation of the vessel itself and of the plant installed on it caused unaccustomed vibrations. These, together with relative movements between the various components of the deck assembly, made for unfavourable observing conditions, especially when the scanner had to stand on steel gratings rather than upon relatively solid superstructure.
Naturally, tropical conditions of temperature and humidity also did nothing to assist the comfort of the team, the survey instruments or their portable computers. At times the temperature exceeded the scanners’ published upper limit of 40ºC, but in fact we were still able to achieve acceptable measurements by simply switching the instrument off and letting it cool down for a few minutes. The very congested environment also made the task difficult, with poor inter-visibility requiring large numbers of instrument stations, often in awkward positions, and a distribution of control targets which was hardly ideal.
Successful Outcome
Despite all the practical challenges, the project was successfully completed within the six-week schedule. There was a one-week preparatory meeting and work planning, followed by three weeks on site, including travelling time from Belgium to Angola. One week of post-processing included combining the datasets, cleaning point-clouds and exporting the data in DGN and IPS formats; and finally a week was spent installing the results on the client’s system and assisting them with possible modelling to adjust the PDS model.
These results form the basis for extensive engineering design work by Sofresid Aquitaine (a member of the Saipem Group), who are using the 3D models to plan, design and compute the details of the new installations, steel structures and pipeline networks on FPSO Girassol. Thanks to these new installations, Total Exploration Production Angola will soon be able to exploit new oilfields in the area, doubling the current production without the need to acquire an additional vessel.
A Promising Future
In general, laser scanning produces a survey that is both quicker and more detailed than would be produced using traditional methods. This directly affects the duration and cost of projects. This is of especial significance where a plant has to be shut down or immobilised at an hourly cost greatly in excess of that paid for high-tech survey equipment, such as 3D laser scanners.
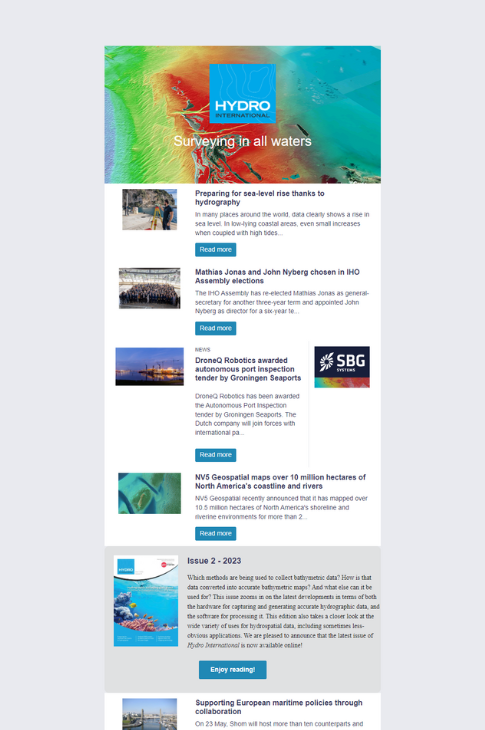
Value staying current with hydrography?
Stay on the map with our expertly curated newsletters.
We provide educational insights, industry updates, and inspiring stories from the world of hydrography to help you learn, grow, and navigate your field with confidence. Don't miss out - subscribe today and ensure you're always informed, educated, and inspired by the latest in hydrographic technology and research.
Choose your newsletter(s)