Conversion from High Seas Patrol to a Hydrographic Ship
The speed in the development of new survey systems, their high acquisition costs and precision installation requirements, combined with the need to mount them on board vessels which are executing hydrographic activities, has moved the Chilean naval authorities to convert a high sea patrol ship into a hydrographic ship.
The project considered the incorporation of a multibeam echo sounder system for shallow and medium depth waters besides other sensors and equipment, including a hydrographic launch, which required the execution of a series of structural transformations in the hull and in the internal configuration of the vessel’s compartments, keeping the vessel’s stability and the hull resistant to the speed of advance, due to the need to place a dome for the multibeam echo sounder transducers.
The Ship to be converted was a High Seas Patrol Ship TAITAO Type of the Chilean Navy, constructed in 1996 by the Chilean Navy Shipyard (ASMAR), with a displacement of 520 Tons, 42.5 metres length and 8.5 metres mould breadth. Her medium draft was 2.95 metres and maximum design speed 15 knots. She is equipped with: two diesel propulsion engines with 1280 hp each; two true screws; two principal electrical generators providing the main general power of 380 Volts, 50 Hz and also other power requirements (220, 115 and 24 Volts); and one auxiliary generator. The capacity for transporting passengers, besides the crew was 18 persons (ship-wrecked) and 12 extra persons when the ship was commissioned to achieve a specific task or special activity.
Equipment to Be Installed
The Chilean Navy Hydrographic and Oceanographic Service (SHOA) organisation has as its principal mission, the provision of technical elements, information and technical assistance to improve safety of navigation and to achieve international standards of precision required for the construction of the nautical charts, either electronic or paper, following the specifications of the International Hydrographic Organisation (IHO). SHOA defined and decided that the multibeam echo sounder system to be installed in the PSG Cabrales would be supplied by STN Atlas Marine Electronics (Germany).
The system included the following components:
Multibeam Echo Sounders
- Atlas Fansweep 20 echo sounder for shallow waters: 200 kHz frequency ; maximum depth up to 300m; coverage up to 12 times the vertical depth, depending on bottom conditions and water depth; up to 1,440 depth values per sweep; beam angles 1.3°; stabilisation of the beams by roll, pitch and heave; processes values of amplitude; 4096 pixels per sweep (side-scan sonar mode); ±0.05 + 0.2 per cent of the vertical depth exactitude
- Atlas Hydrosweep MD-2 echo sounder for medium depth waters: 50 kHz frequency; maximum depth up to 1500m; maximum angle of sweep 152°; coverage up to eight times the vertical depth; 320 depth values per sweep; beam angles between 1° and 2°; stabilisation of the beams by roll, pitch and heave; processes values of amplitude; 2,048 pixels per sweep (side-scan sonar mode); backscatter analysis; 0.3 per cent of the medium vertical depth exactitude
Other components of the system:
- Atlas Deso 25 single beam, double frequency echo sounder for depths up to 3,000 m
- Sound velocity probe SVP-10 for permanent automatic input of the sound velocity measurement at the transducers (C-Keel, located at the dome)
- Sound velocity probe SVP-20 for automatic input of the sound velocity measurement to be paid out and in
- Anschutz Compass Standard 20 Gyro and Anschutz automatic pilot, Nautopilot 2010
- DGPS Ashtech Z12-RTK system and Aanderaa tide gauge system
- Motion sensor Atlas Dynabase - CRU
- Bridge helmsman display
- Wesmar HD 800/160-6 double beam directional echo sounder with retractable transducer
- Acquisition pre-/post-process onboard system, consisting of one workstation for the survey operator (online) and one workstation for the pre-/post- processing (offline)
- Atlas Hydromap Online software: obtains onboard in real time simultaneously, the map and the storage of the data from the multibeam and single-beam echo sounders. Additionally, the software Hydromap Online includes the necessary functions for the control and operation of the multibeam and single-beam echo sounders. It is installed on the survey operator workstation and in the pre-/post-processing workstation. In case of failure of the survey operator workstation, the pre-/post-processing workstation can be used as a substitute
- Atlas Hydromap Offline/CARIS HIPS software: manages, edits, corrects and post-processes the data from the multibeam and single-beam echo sounders. It is installed in the pre-/post-processing work-station and allows the verification of the hydrographic data, correction and post-processing, simultaneously while the acquisition of the data is taking place on the survey operator workstation
- Uninterruptable power supply UPS; A4 ink-jet printer and A0 colour plotter
Additional Equipment: An automated fire extinguishing system; hands-free intercommunications system; a local area network; an existing side-scan sonar Klein 595, and an air treatment unit were also considered to be installed as part of the system.
Hydrographic Launch
One hydrographic launch PUMAR 690 Type, constructed in 2001 by ASMAR, with 6.9 metres length and 2.7 metres mould breadth, speed 8.5 knots; two diesel propulsion engines 40 hp and one electrical generator. Four persons capacity, 2,760 kg. weight. Equipped with an Atlas Deso 17 single beam, double frequency echo sounder for depths up to 1,600m; Atlas Hydromap Susy software for planning, execution and data post processing; one computer and a DGPS Ashtech Z12-RTK system.
Structural Modifications
A dome was designed to be installed under the ship’s keel to allocate the transducers of the multibeam echo sounder system, the hydrographic and ship’s echo sounders and a fixed sound velocity probe sensor, to avoid the turbulence generated by the ship’s hull during her displacement. The dome design was tested at Potsdam and built in Germany under the supervision of STN Atlas Marine Electronics with 4.8m length, 1.3m breadth and 1.2m pillar. This was the biggest change and the most difficult task to carry out during the conversion process.
Besides the dome, other additional equipment was installed. The hydro-graphic launch and its layer; a special winch located at the stern for the sound velocity probe SVP-20; a stern davit with its sheave and a winch with 600m of cable to tow the side-scan sonar. Also, a forward-looking sonar was considered to be installed forward, modifying the hull and some internal compartments, to allocate its retractable transducer operated by a hydraulic mechanism which can bring the transducer into the hull in two seconds. The installation of the dome also meant moving forward the ship’s log.
The place selected to install all of the main controlling units for the components of the multibeam echo sounder system was the shipwrecked living quarters, located at Deck 2.
Stability Effects
Taking into account that the incorporation of a dome and new equipment to the ship would mean a variation of the stability conditions, an evaluation was made to find out its effect. The results obtained by using the proper software tools were that in the light displacement condition, the stability reserve was incremented.
For all the other load conditions, the evaluated parameters were slightly reduced compared to the original load conditions. This can be explained by considering the increment of the displacement and due to this a decrease of the cross curves. In general terms, the installation of the equipment described above did not produce a significant reduction in the ship’s stability.
Hull’s Resistance Effects
To evaluate the effect on the advance resistance, due to the installation of a dome under the hull, a complete analysis was done on the results obtained in a test channel, to a hull with the same characteristics of the PSG Cabrales, performed in December 1994 by the Chilean Austral University. In the final navigation tests at sea, no increment in hull resistance was detected and consequently no reduction of the ship’s speed was experienced. Due to the incorporation of the equipment, structural modifications and the dome installation, one of the main operational changes was the ship’s final draft of 4.12 metres.
Modification to the Interior Departments
The internal disposition of the bridge was modified in order to install the display and controlling unit of the forward looking sonar; the helmsman display of the multibeam echo sounder system, the hands-free intercommunication system and the Nautopilot controlling unit.
The shipwrecked living quarters, located at Deck 2 were converted into the Hydrographic Room, inside of which all the controlling units of the multibeam echo sounder system, DGPS, tide gauge, sound velocity probe converter box, side-scan sonar consoles, UPS, plotter, printer and online / offline workstations were placed.
The automated fire extinguishing system’s detectors; hands-free inter-communications system; the local area network; air treatment unit; special power sockets and switching units for different voltages; a chart working light table, workstations desks and special chairs; appropriate furniture to store charts, manuals, etc; special lashings for each device, etc, were also installed.
Summary
- The conversion of this type of High Seas Patrol Ship into a Hydro-graphic Ship was possible and executed with success due to the technological development of ASMAR in a co-ordinated project with SHOA which spent more than a year planning every single detail to allow the conversion process to take place in a short period and with the minimum interference, faithfully following the hydrographic and structural requirements which were formulated at the beginning of the project
- The conversion process was not an easy task. Lots of studies, meetings, simulations, travelling, and exchange of information with the system designers and factory professionals and technicians were conducted, and almost a hundred different detailed and general engineering drawings were made. To accomplish this task successfully, the Special Projects Office of SHOA, dedicated almost all of its human resources exclusively to this project
- The PSG Cabrales with these modifications, the installation of the dome and other associated equipment, practically did not change her stability and velocity conditions, gaining a highly modern hydrographic capability
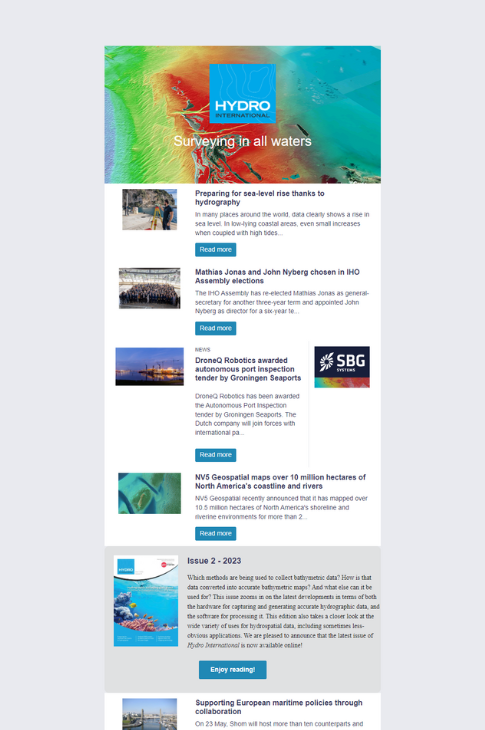
Value staying current with hydrography?
Stay on the map with our expertly curated newsletters.
We provide educational insights, industry updates, and inspiring stories from the world of hydrography to help you learn, grow, and navigate your field with confidence. Don't miss out - subscribe today and ensure you're always informed, educated, and inspired by the latest in hydrographic technology and research.
Choose your newsletter(s)